论文标题:《机械工程前沿》2021年第四期摘要
期刊: Frontiers of Mechanical Engineering
微信链接:点击此处阅读微信文章
01
Review Article
Cryogenic minimum quantity lubrication machining: from mechanism to application
文章引用:
Mingzheng LIU, Changhe LI, Yanbin ZHANG, Qinglong AN, Min YANG, Teng GAO, Cong MAO, Bo LIU, Huajun CAO, Xuefeng XU, Zafar SAID, Sujan DEBNATH, Muhammad JAMIL, Hafz Muhammad ALI, Shubham SHARMA. Cryogenic minimum quantity lubrication machining: from mechanism to application. Front. Mech. Eng., 2021, 16(4): 649–697
https://doi.org/10.1007/s11465-021-0654-2
文章摘要:
Cutting fluid plays a cooling–lubrication role in the cutting of metal materials. However, the substantial usage of cutting fluid in traditional flood machining seriously pollutes the environment and threatens the health of workers. Environmental machining technologies, such as dry cutting, minimum quantity lubrication (MQL), and cryogenic cooling technology, have been used as substitute for flood machining. However, the insufficient cooling capacity of MQL with normal-temperature compressed gas and the lack of lubricating performance of cryogenic cooling technology limit their industrial application. The technical bottleneck of mechanical–thermal damage of difficult-to-cut materials in aerospace and other fields can be solved by combining cryogenic medium and MQL. The latest progress of cryogenic minimum quantity lubrication (CMQL) technology is reviewed in this paper, and the key scientific issues in the research achievements of CMQL are clarified. First, the application forms and process characteristics of CMQL devices in turning, milling, and grinding are systematically summarized from traditional settings to innovative design. Second, the cooling–lubrication mechanism of CMQL and its influence mechanism on material hardness, cutting force, tool wear, and workpiece surface quality in cutting are extensively revealed. The effects of CMQL are systematically analyzed based on its mechanism and application form. Results show that the application effect of CMQL is better than that of cryogenic technology or MQL alone. Finally, the prospect, which provides basis and support for engineering application and development of CMQL technology, is introduced considering the limitations of CMQL.
文章链接:
https://journal.hep.com.cn/fme/EN/10.1007/s11465-021-0654-2
02
Research Article
1. Development of a redundant anthropomorphic hydraulically actuated manipulator with a roll–pitch–yaw spherical wrist
文章引用:
Min CHENG, Zenan HAN, Ruqi DING, Junhui ZHANG, Bing XU. Development of a redundant anthropomorphic hydraulically actuated manipulator with a roll–pitch–yaw spherical wrist. Front. Mech. Eng., 2021, 16(4): 698–710
https://doi.org/10.1007/s11465-021-0646-2
文章摘要:
The demand for redundant hydraulic manipulators that can implement complex heavy-duty tasks in unstructured areas is increasing; however, current manipulator layouts that remarkably differ from human arms make intuitive kinematic operation challenging to achieve. This study proposes a seven-degree-of-freedom (7-DOF) redundant anthropomorphic hydraulically actuated manipulator with a novel roll–pitch–yaw spherical wrist. A hybrid series–parallel mechanism is presented to achieve the spherical wrist design, which consists of two parallel linear hydraulic cylinders to drive the yaw/pitch 2-DOF wrist plate connected serially to the roll structure. Designed as a 1R PRRR-1S PU mechanism (“R”, “P”, “S”, and “U” denote revolute, prismatic, spherical, and universal joints, respectively; the underlined letter indicates the active joint), the 2-DOF parallel structure is partially decoupled to obtain simple forward/inverse kinematic solutions in which a closed-loop subchain “R PRR” is included. The 7-DOF manipulator is then designed, and its third joint axis goes through the spherical center to obtain closed-form inverse kinematic computation. The analytical inverse kinematic solution is drawn by constructing self-motion manifolds. Finally, a physical prototype is developed, and the kinematic analysis is validated via numerical simulation and test results.
文章链接:
https://journal.hep.com.cn/fme/EN/10.1007/s11465-021-0646-2
2. Mechanical design and analysis of a novel variable stiffness actuator with symmetrical pivot adjustment
文章引用:
Yiwei LIU, Shipeng CUI, Yongjun SUN. Mechanical design and analysis of a novel variable stiffness actuator with symmetrical pivot adjustment. Front. Mech. Eng., 2021, 16(4): 711–725
https://doi.org/10.1007/s11465-021-0647-1
文章摘要:
The safety of human–robot interaction is an essential requirement for designing collaborative robotics. Thus, this paper aims to design a novel variable stiffness actuator (VSA) that can provide safer physical human–robot interaction for collaborative robotics. VSA follows the idea of modular design, mainly including a variable stiffness module and a drive module. The variable stiffness module transmits the motion from the drive module in a roundabout manner, making the modularization of VSA possible. As the key component of the variable stiffness module, a stiffness adjustment mechanism with a symmetrical structure is applied to change the positions of a pair of pivots in two levers linearly and simultaneously, which can eliminate the additional bending moment caused by the asymmetric structure. The design of the double-deck grooves in the lever allows the pivot to move freely in the groove, avoiding the geometric constraint between the parts. Consequently, the VSA stiffness can change from zero to infinity as the pivot moves from one end of the groove to the other. To facilitate building a manipulator in the future, an expandable electrical system with a distributed structure is also proposed. Stiffness calibration and control experiments are performed to evaluate the physical performance of the designed VSA. Experiment results show that the VSA stiffness is close to the theoretical design stiffness. Furthermore, the VSA with a proportional–derivative feedback plus feedforward controller exhibits a fast response for stiffness regulation and a good performance for position tracking.
文章链接:
https://journal.hep.com.cn/fme/EN/10.1007/s11465-021-0647-1
3. Optimum design and preliminary experiments of a novel parallel end traction apparatus for upper-limb rehabilitation
文章引用:
Shiping ZUO, Jianfeng LI, Mingjie DONG, Guotong LI, Yu ZHOU. Optimum design and preliminary experiments of a novel parallel end traction apparatus for upper-limb rehabilitation. Front. Mech. Eng., 2021, 16(4): 726–746
https://doi.org/10.1007/s11465-021-0651-5
文章摘要:Robot-assisted technology has been increasingly employed in the therapy of post stroke patients to deliver high-quality treatment and alleviate therapists’ burden. This paper introduces a novel parallel end traction apparatus (PETA) to supplement equipment selection. Considering the appearance and performance of the PETA, two types of special five-bar linkage mechanisms are selected as the potential configurations of the actuation execution unit because of their compact arrangement and parallel structure. Kinematic analysis of each mechanism, i.e., position solutions and Jacobian matrix, is carried out. Subsequently, a comparative study between the two mechanisms is conducted. In the established source of nondimensional parameter synthesis, the singularity, maximum continuous workspace, and performance variation trends are analyzed. Based on the evaluation results, the final scheme with determined configuration and corresponding near-optimized nondimensional parameters is obtained. Then, a prototype is constructed. By adding a lockable translational degree of freedom in the vertical direction, the PETA can provide 2D planar exercise and 3D spatial exercise. Finally, a control system is developed for passive exercise mode based on the derived inverse position solution, and preliminary experiments are performed to verify the applicability of the PETA.
文章链接:
https://journal.hep.com.cn/fme/EN/10.1007/s11465-021-0651-5
4. Design method and verification of a hybrid prosthetic mechanism with energy-damper clutchable device for transfemoral amputees
文章引用:
Majun SONG, Sheng GUO, Anderson S. OLIVEIRA, Xiangyang WANG, Haibo QU. Design method and verification of a hybrid prosthetic mechanism with energy-damper clutchable device for transfemoral amputees. Front. Mech. Eng., 2021, 16(4): 747–764
https://doi.org/10.1007/s11465-021-0644-4
文章摘要:
Transfemoral amputees (TAs) have difficulty in mobility during walking, such as restricted movement of lower extremity and body instability, yet few transfemoral prostheses have explored human-like multiple motion characteristics by simple structures to fit the kinesiology, biomechanics, and stability of human lower extremity. In this work, the configurations of transfemoral prosthetic mechanism are synthesized in terms of human lower-extremity kinesiology. A hybrid transfemoral prosthetic (HTP) mechanism with multigait functions is proposed to recover the gait functions of TAs. The kinematic and mechanical performances of the designed parallel mechanism are analyzed to verify their feasibility in transfemoral prosthetic mechanism. Inspired by motion–energy coupling relationship of the knee, a wearable energy-damper clutched device that can provide energy in knee stance flexion to facilitate the leg off from the ground and can impede the leg’s swing velocity for the next stance phase is proposed. Its co-operation with the springs in the prismatic pairs enables the prosthetic mechanism to have the energy recycling ability under the gait rhythm of the knee joint. Results demonstrate that the designed HTP mechanism can replace the motion functions of the knee and ankle to realize its multimode gait and effectively decrease the peak power of actuators from 94.74 to 137.05 W while maintaining a good mechanical adaptive stability.
文章链接:
https://journal.hep.com.cn/fme/EN/10.1007/s11465-021-0644-4
5. Design and analysis of the gripper mechanism based on generalized parallel mechanisms with configurable moving platform
文章引用:
Lin WANG, Yuefa FANG, Luquan LI. Design and analysis of the gripper mechanism based on generalized parallel mechanisms with configurable moving platform. Front. Mech. Eng., 2021, 16(4): 765–781
https://doi.org/10.1007/s11465-021-0655-1
文章摘要:
Generalized parallel mechanisms with a configurable moving platform have become popular in the research field of parallel mechanism. This type of gripper mechanism can be applied to grasp large or heavy objects in different environments that are dangerous and complex for humans. This study proposes a family of novel (5 + 1) degrees of freedom (three translations and two rotations plus an additional grasping motion) gripper mechanisms based on the generalized parallel mechanisms with a configurable moving platform. First, the configurable moving platform, which is a closed loop, is designed for grasping manipulation. The hybrid topological arrangement is determined to improve the stiffness of the manipulator and realize high load-to-weight ratios. A sufficient rule based on Lie group theory is proposed to synthesize the mechanism. The hybrid limb structure is also enumerated. A family of novel gripper mechanisms can be assembled through the hybrid limbs by satisfying the rule. Two examples of the gripper mechanisms with and without parallelogram pairs are shown in this study. A kinematic analysis of the example mechanism is presented. The workspace shows that the mechanism possesses high rotational capability. In addition, a stiffness analysis is performed.
文章链接:
https://journal.hep.com.cn/fme/EN/10.1007/s11465-021-0655-1
6. Isogeometric analysis based on geometric reconstruction models
文章引用:
Yingjun WANG, Liang GAO, Jinping QU, Zhaohui XIA, Xiaowei DENG. Isogeometric analysis based on geometric reconstruction models. Front. Mech. Eng., 2021, 16(4): 782–797
https://doi.org/10.1007/s11465-021-0648-0
文章摘要:
In isogeometric analysis (IGA), the boundary representation of computer-aided design (CAD) and the tensor-product non-uniform rational B-spline structure make the analysis of three-dimensional (3D) problems with irregular geometries difficult. In this paper, an IGA method for complex models is presented by reconstructing analysis-suitable models. The CAD model is represented by boundary polygons or point cloud and is embedded into a regular background grid, and a model reconstruction method is proposed to obtain the level set function of the approximate model, which can be directly used in IGA. Three 3D examples are used to test the proposed method, and the results demonstrate that the proposed method can deal with complex engineering parts reconstructed by boundary polygons or point clouds.
文章链接:
https://journal.hep.com.cn/fme/EN/10.1007/s11465-021-0648-0
7. Group-based multiple pipe routing method for aero-engine focusing on parallel layout
文章引用:
Hexiang YUAN, Jiapeng YU, Duo JIA, Qiang LIU, Hui MA. Group-based multiple pipe routing method for aero-engine focusing on parallel layout. Front. Mech. Eng., 2021, 16(4): 798–813
https://doi.org/10.1007/s11465-021-0645-3
文章摘要:
External pipe routing for aero-engine in limited three-dimensional space is a typical nondeterministic polynomial hard problem, where the parallel layout of pipes plays an important role in improving the utilization of layout space, facilitating pipe assembly, and maintenance. This paper presents an automatic multiple pipe routing method for aero-engine that focuses on parallel layout. The compressed visibility graph construction algorithm is proposed first to determine rapidly the rough path and interference relationship of the pipes to be routed. Based on these rough paths, the information of pipe grouping and sequencing are obtained according to the difference degree and interference degree, respectively. Subsequently, a coevolutionary improved differential evolution algorithm, which adopts the coevolutionary strategy, is used to solve multiple pipe layout optimization problem. By using this algorithm, pipes in the same group share the layout space information with one another, and the optimal layout solution of pipes in this group can be obtained in the same evolutionary progress. Furthermore, to eliminate the minor angle deviation of parallel pipes that would cause assembly stress in actual assembly, an accurate parallelization processing method based on the simulated annealing algorithm is proposed. Finally, the simulation results on an aero-engine demonstrate the feasibility and effectiveness of the proposed method.
文章链接:
https://journal.hep.com.cn/fme/EN/10.1007/s11465-021-0645-3
8. Deep convolutional tree-inspired network: a decision-tree-structured neural network for hierarchical fault diagnosis of bearings
文章引用:
Xu WANG, Hongyang GU, Tianyang WANG, Wei ZHANG, Aihua LI, Fulei CHU. Deep convolutional tree-inspired network: a decision-tree-structured neural network for hierarchical fault diagnosis of bearings. Front. Mech. Eng., 2021, 16(4): 814–828
https://doi.org/10.1007/s11465-021-0650-6
文章摘要:
The fault diagnosis of bearings is crucial in ensuring the reliability of rotating machinery. Deep neural networks have provided unprecedented opportunities to condition monitoring from a new perspective due to the powerful ability in learning fault-related knowledge. However, the inexplicability and low generalization ability of fault diagnosis models still bar them from the application. To address this issue, this paper explores a decision-tree-structured neural network, that is, the deep convolutional tree-inspired network (DCTN), for the hierarchical fault diagnosis of bearings. The proposed model effectively integrates the advantages of convolutional neural network (CNN) and decision tree methods by rebuilding the output decision layer of CNN according to the hierarchical structural characteristics of the decision tree, which is by no means a simple combination of the two models. The proposed DCTN model has unique advantages in 1) the hierarchical structure that can support more accuracy and comprehensive fault diagnosis, 2) the better interpretability of the model output with hierarchical decision making, and 3) more powerful generalization capabilities for the samples across fault severities. The multiclass fault diagnosis case and cross-severity fault diagnosis case are executed on a multicondition aeronautical bearing test rig. Experimental results can fully demonstrate the feasibility and superiority of the proposed method.
文章链接:
https://journal.hep.com.cn/fme/EN/10.1007/s11465-021-0650-6
9. Imbalanced fault diagnosis of rotating machinery using autoencoder-based SuperGraph feature learning
文章引用:
Jie LIU, Kaibo ZHOU, Chaoying YANG, Guoliang LU. Imbalanced fault diagnosis of rotating machinery using autoencoder-based SuperGraph feature learning. Front. Mech. Eng., 2021, 16(4): 829–839
https://doi.org/10.1007/s11465-021-0652-4
文章摘要:
Existing fault diagnosis methods usually assume that there are balanced training data for every machine health state. However, the collection of fault signals is very difficult and expensive, resulting in the problem of imbalanced training dataset. It will degrade the performance of fault diagnosis methods significantly. To address this problem, an imbalanced fault diagnosis of rotating machinery using autoencoder-based SuperGraph feature learning is proposed in this paper. Unsupervised autoencoder is firstly used to compress every monitoring signal into a low-dimensional vector as the node attribute in the SuperGraph. And the edge connections in the graph depend on the relationship between signals. On the basis, graph convolution is performed on the constructed SuperGraph to achieve imbalanced training dataset fault diagnosis for rotating machinery. Comprehensive experiments are conducted on a benchmarking publicized dataset and a practical experimental platform, and the results show that the proposed method can effectively achieve rotating machinery fault diagnosis towards imbalanced training dataset through graph feature learning.
文章链接:
https://journal.hep.com.cn/fme/EN/10.1007/s11465-021-0652-4
10. Fractal characteristic evaluation and interpolation reconstruction for surface topography of drilled composite hole wall
文章引用:
Yu YANG, Hui CHENG, Biao LIANG, Guoyi HOU, Di ZHAO, Chun LIU, Kaifu ZHANG. Fractal characteristic evaluation and interpolation reconstruction for surface topography of drilled composite hole wall. Front. Mech. Eng., 2021, 16(4): 840–854
https://doi.org/10.1007/s11465-021-0643-5
文章摘要:
In this paper, an improved fractal interpolation model is proposed to reconstruct the surface topography of composite hole wall. This model adopts the maximum positive deviations and maximum negative deviations between the measured values and trend values to determine the contraction factors. Hole profiles in 24 directions are measured. Fractal parameters are calculated to evaluate the measured surface profiles. The maximum and minimum fractal dimension of the hole wall are 1.36 and 1.07, whereas the maximum and minimum fractal roughness are 4.05 × 10 −5 and 4.36 × 10 −10 m, respectively. Based on the two-dimensional evaluation results, three-dimensional surface topographies in five typical angles (0°, 45°, 90°, 135°, and 165°) are reconstructed using the improved model. Fractal parameter D s and statistical parameters Sa, Sq, and Sz are used to evaluate the reconstructed surfaces. Average error of D s, Sa, Sq, and Sz between the measured surfaces and the reconstructed surfaces are 1.53%, 3.60%, 5.60%, and 9.47%, respectively. Compared with the model in published literature, the proposed model has equal reconstruction effect in relatively smooth surface and is more advanced in relatively rough surface. Comparative results prove that the proposed model for calculating contraction factors is more reasonable.
文章链接:
https://journal.hep.com.cn/fme/EN/10.1007/s11465-021-0643-5
11. Position-varying surface roughness prediction method considering compensated acceleration in milling of thin-walled workpiece
文章引用:
Zequan YAO, Chang FAN, Zhao ZHANG, Dinghua ZHANG, Ming LUO. Position-varying surface roughness prediction method considering compensated acceleration in milling of thin-walled workpiece. Front. Mech. Eng., 2021, 16(4): 855–867
https://doi.org/10.1007/s11465-021-0649-z
文章摘要:
Machined surface roughness will affect parts’ service performance. Thus, predicting it in the machining is important to avoid rejects. Surface roughness will be affected by system position dependent vibration even under constant parameter with certain toolpath processing in the finishing. Aiming at surface roughness prediction in the machining process, this paper proposes a position-varying surface roughness prediction method based on compensated acceleration by using regression analysis. To reduce the stochastic error of measuring the machined surface profile height, the surface area is repeatedly measured three times, and Pauta criterion is adopted to eliminate abnormal points. The actual vibration state at any processing position is obtained through the single-point monitoring acceleration compensation model. Seven acceleration features are extracted, and valley, which has the highest R-square proving the effectiveness of the filtering features, is selected as the input of the prediction model by mutual information coefficients. Finally, by comparing the measured and predicted surface roughness curves, they have the same trends, with the average error of 16.28% and the minimum error of 0.16%. Moreover, the prediction curve matches and agrees well with the actual surface state, which verifies the accuracy and reliability of the model.
文章链接:
https://journal.hep.com.cn/fme/EN/10.1007/s11465-021-0649-z
12. An energy consumption prediction approach of die casting machines driven by product parameters
文章引用:
Erheng CHEN, Hongcheng LI, Huajun CAO, Xuanhao WEN. An energy consumption prediction approach of die casting machines driven by product parameters. Front. Mech. Eng., 2021, 16(4): 868–886
https://doi.org/10.1007/s11465-021-0656-0
文章摘要:
Die casting machines, which are the core equipment of the machinery manufacturing industry, consume great amounts of energy. The energy consumption prediction of die casting machines can support energy consumption quota, process parameter energy-saving optimization, energy-saving design, and energy efficiency evaluation; thus, it is of great significance for Industry 4.0 and green manufacturing. Nevertheless, due to the uncertainty and complexity of the energy consumption in die casting machines, there is still a lack of an approach for energy consumption prediction that can provide support for process parameter optimization and product design taking energy efficiency into consideration. To fill this gap, this paper proposes an energy consumption prediction approach for die casting machines driven by product parameters. Firstly, the system boundary of energy consumption prediction is defined, and subsequently, based on the energy consumption characteristics analysis, a theoretical energy consumption model is established. Consequently, a systematic energy consumption prediction approach for die casting machines, involving product, die, equipment, and process parameters, is proposed. Finally, the feasibility and reliability of the proposed energy consumption prediction approach are verified with the help of three die casting machines and six types of products. The results show that the prediction accuracy of production time and energy consumption reached 91.64% and 85.55%, respectively. Overall, the proposed approach can be used for the energy consumption prediction of different die casting machines with different products.
文章链接:
https://journal.hep.com.cn/fme/EN/10.1007/s11465-021-0656-0
13. Coordinated shift control of nonsynchronizer transmission for electric vehicles based on dynamic tooth alignment
文章引用:
Xiaotong XU, Yutao LUO, Xue HAO. Coordinated shift control of nonsynchronizer transmission for electric vehicles based on dynamic tooth alignment. Front. Mech. Eng., 2021, 16(4): 887–900
https://doi.org/10.1007/s11465-021-0653-3
文章摘要:
Multispeed transmissions can enhance the dynamics and economic performance of electric vehicles (EVs), but the coordinated control of the drive motor and gear shift mechanism during gear shifting is still a difficult challenge because gear shifting may cause discomfort to the occupants. To improve the swiftness of gear shifting, this paper proposes a coordinated shift control method based on the dynamic tooth alignment (DTA) algorithm for nonsynchronizer automated mechanical transmissions (NSAMTs) of EVs. After the speed difference between the sleeve (SL) and target dog gear is reduced to a certain value by speed synchronization, angle synchronization is adopted to synchronize the SL quickly to the target tooth slot’s angular position predicted by the DTA. A two-speed planetary NSAMT is taken as an example to carry out comparative simulations and bench experiments. Results show that gear shifting duration and maximum jerk are reduced under the shift control with the proposed method, which proves the effectiveness of the proposed coordinated shift control method with DTA.
文章链接:
https://journal.hep.com.cn/fme/EN/10.1007/s11465-021-0653-3
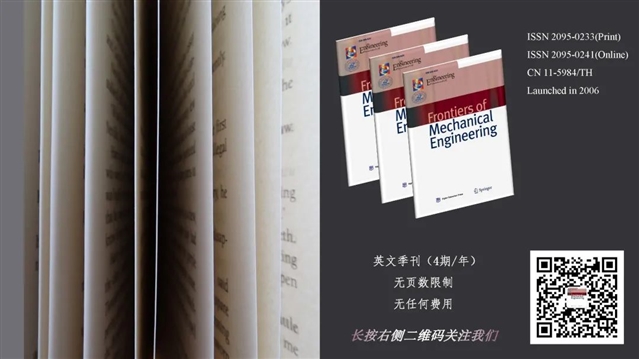
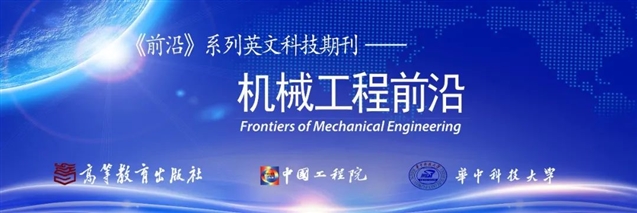
《前沿》系列英文学术期刊
由教育部主管、高等教育出版社主办的《前沿》(Frontiers)系列英文学术期刊,于2006年正式创刊,以网络版和印刷版向全球发行。系列期刊包括基础科学、生命科学、工程技术和人文社会科学四个主题,是我国覆盖学科最广泛的英文学术期刊群,其中13种被SCI收录,其他也被A&HCI、Ei、MEDLINE或相应学科国际权威检索系统收录,具有一定的国际学术影响力。系列期刊采用在线优先出版方式,保证文章以最快速度发表。
中国学术前沿期刊网
http://journal.hep.com.cn
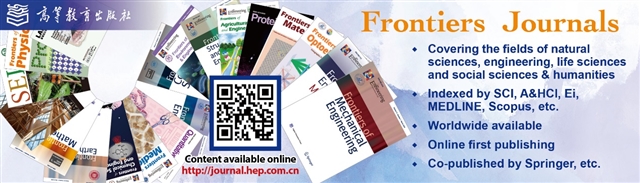
特别声明:本文转载仅仅是出于传播信息的需要,并不意味着代表本网站观点或证实其内容的真实性;如其他媒体、网站或个人从本网站转载使用,须保留本网站注明的“来源”,并自负版权等法律责任;作者如果不希望被转载或者联系转载稿费等事宜,请与我们接洽。